С помощью черновых и чистовых операций, выполняемых на токарных станках, получают детали различной конфигурации с показателем чистоты поверхности Ra до 1,25, а в некоторых случаях и выше. Точность поверхности зависит от жесткости системы станок-инструмент-деталь, от применяемого инструмента и режимов резания: чем тверже режущая кромка инструмента (твердые сплавы, металлокерамика, эльбор, алмаз), выше скорость вращения заготовки, меньше подача и вылет резца, тем лучше показатели чистоты и точности поверхности.

Универсальный токарный станок CDS6250
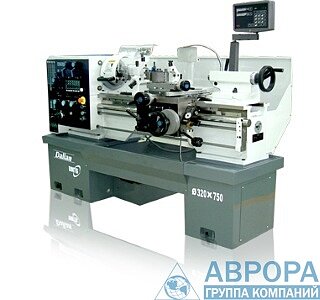
Винторезный универсальный токарный станок CDS6132
К видам работ, производимых на универсальных токарных станках, относят:
- растачивание отверстий;
- сверление, зенкерование, развертывание отверстий;
- нарезание внутренней и наружной резьбы с помощью резцов и инструмента: плашек, метчиков, резьбонарезных головок;
- обточку конических деталей типа вал;
- обработку цилиндрических поверхностей;
- торцовку заготовок, обработку уступов;
- вытачивание канавок, отрезку;
- оформление сложных поверхностей тел вращения, фасонное точение.
Растачивание отверстий
Получение ступенчатых отверстий большого диаметра, а также внутренних канавок возможно с помощью операции растачивания. Изделие зажимается в патрон передней бабки, поддерживается люнетом (в случае значительной длины). При этом, доступ к торцу, обрабатываемому расточным резцом, остается свободен. Точность расточки на универсальном токарном станке часто обеспечивается технологией расточки, режущим инструментом, опытом токаря и техническим состоянием оборудования. Перемещение физически осуществляется помощью лимбов поперечного и продольного перемещений, с отображением координат на УЦИ
Сверление, зенкерование, развертывание отверстий
Обработку можно производить как по центру детали (при зажиме ее в трехкулачковом патроне), так и со смещением центра отверстия. Смещение (эксцентриситет) достигается фиксацией заготовки в четырехкулачковом токарном патроне или на планшайбе передней бабки.
Обрабатывающий инструмент: зенкер, сверло, развертка — закрепляется в коническом отверстии задней бабки напрямую или через зажимной патрон. Для точности токарной обработки необходима правильная и одинаковая заточка режущих кромок сверла. Также важна перпендикулярность торца заготовки оси инструмента, отсутствие заусенцев, неровностей поверхности. Подача инструмента происходит вручную или механически. Сверло обеспечивает чистоту поверхности отверстия Ra 6.3…3.2, зенкер — Ra 2.5, развертка — Ra 1.25…0,8.
Нарезание внутренней и наружной резьбы с помощью резцов и инструмента: плашек, метчиков, резьбонарезных головок
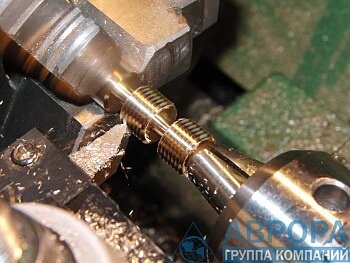
Обточка конических деталей типа вал
Способов токарной обработки конической поверхности несколько. Их выбор зависит от конфигурации детали и угла конуса.
- Формирование поверхности конуса (как наружной, так и конического отверстия) можно обеспечить поворотом поперечного суппорта и использованием его ручной подачи. Необходимый угол высчитывают по формуле: tg α = (D-d)/2L, где D, d, L — это соответственно диаметры и длина конуса. Длина конической части заготовки, получаемой за один цикл токарной обработки, ограничивается величиной хода суппорта.
- При сравнительно небольшой длине обрабатываемого конуса можно использовать поперечную подачу суппорта и резец с пластиной, заточенной под конус. Длина пластины должна немного превосходить величину обрабатываемой поверхности (способ для обработки наружных конусов).
- Точение конической заготовки обеспечивается поперечным смещением задней бабки относительно оси шпинделя (a = L(D-d)/2L, где а — величина смещения). Таким методом изготавливают детали с небольшой конусностью (не более 8 градусов) и значительной длиной.
- Использование копировальной линейки, укрепляемой на станине станка и связанной с его суппортом при помощи ползуна — также один из способов конического точения. Угол между линейкой и осью шпинделя точно равен углу получаемой поверхности.
- Использование конической линейки, взаимозавязывающей перемещение суппорта с величиной продольного перемещения по оси Z
Обработка цилиндрических поверхностей
При токарной обработке цилиндрических поверхностей применяют следующие способы для обеспечения жесткости крепления заготовки и точности точения:
- Фиксация в центрах передней и задней бабки, в пиноль которой, как правило, вставляют вращающийся центр и им поджимают заготовку. Поводковая планшайба передает крутящий момент от шпинделя токарного станка изделию.
- Закрепление деталей со сравнительно небольшой длиной в трех- или четырехкулачковом токарных патронах. Длинные заготовки также могут закрепляться в патроне шпинделя, а их консольная часть при резании поддерживается люнетом. Люнет устанавливается на высокоточные полозья станины.
- Применяют комбинированное (1 и 2) закрепление обрабатываемых изделий.
Разновидность наружного точения — обработка ступенчатых валов с помощью проходных упорных и подрезных резцов, а также формирование канавок, галтелей, фасок. Повысить производительность обработки многоступенчатых валов на универсальных токарных станках позволяет многопозиционный упор для суппорта, настраиваемый по первой детали, или копировальное устройство (копир).
Торцовка заготовок, обработка уступов
Этот вид обработки достижим при закреплении детали как в патроне шпинделя станка, так и в центрах (для задней бабки в этом случае применяют полуцентр). Операция производится подрезными или проходными резцами. Лучшую чистоту поверхности дает обработка «от центра к периферии».
Вытачивание канавок, отрезка
Токарная обработка канавок заготовки ведется прорезными резцами за один или несколько проходов (в зависимости от конфигурации и требуемой точности поверхностей).
Отрезку изделия или заготовки производят отрезными резцами. Поломку инструмента в конце резания предотвращают использованием поддерживающих люнетов и снижением подачи резца (на 45-55%) при приближении его к центру детали на половину радиуса заготовки.
Оформление сложных поверхностей тел вращения, фасонное точение
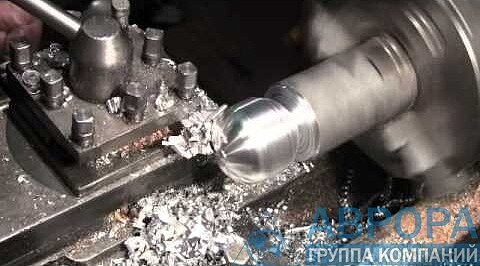
Тела вращения с криволинейной образующей получают путем токарной обработки заготовки:
- проходными резцами с одновременным применением поперечной и продольной подачи (способ характерен для единичного производства, необходима высокая квалификация токаря);
- фасонными резцами, точно повторяющими конфигурацию требуемой поверхности (способ рентабелен при серийном производстве, но ограничивается максимальной шириной резца — порядка 50-60 мм);
- проходными резцами с использованием копира или гидрокопировального суппорта, разновидность такой обработки — точение сферических поверхностей.
Специальные возможности токарных станков
С помощью универсального токарного станка может проводиться обработка шпоночных пазов, отделка поверхностей (полировка, суперфиниширование), доводка (притирка), обкатывание шариками и роликами, накатывание, алмазное выглаживание т.д.